When it comes to construction, the materials used play a crucial role in the overall durability and effectiveness of a project. Among these materials, concrete form plywood has emerged as a favorite for builders. It offers significant advantages, including strength, ease of use, and cost-effectiveness. This article will delve into various essential aspects of concrete form plywood, providing tips for selection, handling, installation, and maintenance.
Understanding Concrete Form Plywood
The Basics of Concrete Form Plywood
Concrete form plywood is specifically designed for use in concrete construction projects. It is manufactured using ultra-durable materials that are resistant to moisture and warping, making it an ideal choice for forming concrete structures. Typically produced with a furnace-dried veneer, this plywood is available in different thicknesses to meet various project needs.
Another important aspect of maintaining concrete form plywood is proper handling during transportation and installation. When moving the sheets, always lift them from the bottom rather than dragging them across surfaces, as this can prevent unnecessary stress and potential damage. Additionally, during installation, ensure that the plywood is adequately supported and secured to avoid any shifting that could compromise its structural integrity. By taking these precautions, you not only protect your investment but also enhance the overall performance of your construction project.
One of the primary purposes of concrete form plywood is to create molds for wet concrete. Once the concrete cures, the plywood is removed, leaving the desired shape. This process not only aids in building foundations and walls but also allows for intricate designs in architectural projects. The versatility of concrete form plywood means it can be used in a variety of applications, from residential homes to large-scale commercial buildings, demonstrating its essential role in modern construction.
Moreover, the use of concrete form plywood can significantly enhance the efficiency of the construction process. By allowing for quick assembly and disassembly, it reduces labor time and increases productivity on the job site. Additionally, the lightweight nature of the plywood makes it easier for workers to handle, further streamlining the workflow. This efficiency is particularly beneficial in projects with tight deadlines, where every moment counts.
Key Features of Concrete Form Plywood
Concrete form plywood boasts several features that set it apart from conventional plywood. Key offerings include:
- Moisture Resistance: Treated to withstand wet conditions, it does not easily swell or warp when exposed to moisture.
- Reusability: High-quality plywood can be reused multiple times, leading to cost savings on repetitive projects.
- Strength and Stability: Engineered for enhanced strength, it resists buckling under heavy loads.
- Surface Smoothness: Provides a smooth finish to the concrete, minimizing the need for extensive finishing work.
In addition to these features, concrete form plywood is often treated with special coatings that enhance its durability and performance. These coatings can provide added protection against the harsh chemicals sometimes found in concrete mixtures, ensuring that the plywood maintains its integrity throughout the curing process. Furthermore, advancements in technology have led to the development of eco-friendly options, allowing builders to choose sustainable materials without compromising on quality or performance. This growing trend towards sustainability reflects a broader commitment within the construction industry to reduce environmental impact while still delivering high-quality results.
Choosing the Right Concrete Form Plywood
Factors to Consider When Selecting Plywood
When selecting concrete form plywood, builders must take several factors into account to ensure the best outcome for their construction projects. Some important considerations include:
- Thickness: The thickness of the plywood should correspond to the expected load and the type of project.
- Grade: Higher-grade plywood is generally more durable, making it suitable for challenging construction applications.
- Manufacturer Reputation: Selecting products from reputed manufacturers can often guarantee quality, performance, and support.
- Cost: While it may be tempting to go for the cheapest option, investing in quality plywood can reduce long-term costs through durability and reusability.
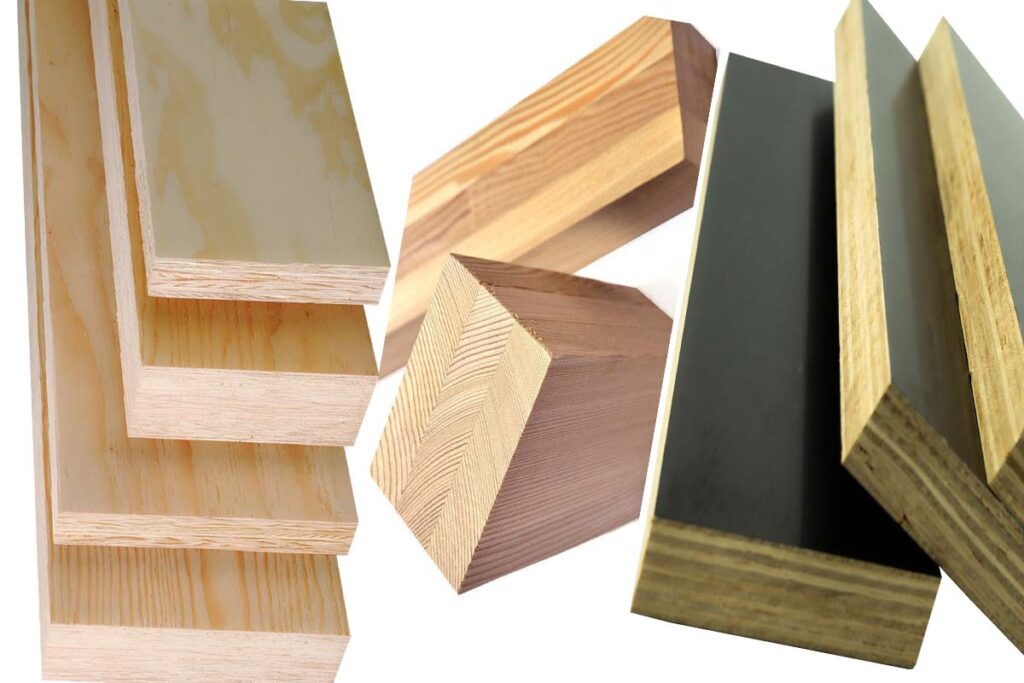
Common Mistakes to Avoid
Choosing the wrong plywood can lead to disastrous project outcomes. Below are some common mistakes builders should avoid:
- Underestimating Load Requirements: Always assess the load requirements accurately; using insufficient thickness can lead to collapse.
- Neglecting Moisture Ratings: Failing to choose plywood suitable for the moisture conditions can result in warping and damage.
- Ignoring Product Reviews: Reviews and feedback can provide invaluable insights into the performance of specific plywood brands.
- Failing to Follow Best Practices: Not adhering to recommended handling and installation practices can compromise the integrity of the project.
Additional Considerations for Project Longevity
In addition to the factors and mistakes outlined above, builders should also consider the long-term implications of their plywood choices. For instance, the environmental impact of the materials used is becoming increasingly important in today’s construction landscape. Opting for sustainably sourced plywood not only helps in reducing the carbon footprint but can also enhance the project’s appeal to environmentally conscious clients. Furthermore, the treatment of the plywood can play a significant role in its longevity; using water-resistant or chemically treated options can provide additional protection against the elements, ensuring that the forms maintain their shape and integrity over multiple uses. Find more about environmental on https://www.epa.gov/education/what-environmental-education
Another aspect to keep in mind is the ease of installation and removal. Plywood that is easier to handle can significantly reduce labor costs and time on-site. Builders should look for features such as lightweight construction or pre-drilled holes that facilitate quicker assembly. Additionally, considering the reusability of the plywood can lead to significant savings in future projects. Choosing high-quality, durable plywood can allow for multiple uses, making it a wise investment for contractors looking to optimize their resources over time.
Proper Handling and Storage of Concrete Form Plywood
Tips for Handling Plywood Safely
Handling concrete form plywood correctly is essential to maintain its quality and performance. Here are some safety tips:
- Use Protective Gear: Always wear gloves, goggles, and appropriate footwear when handling plywood to prevent injuries.
- Lift with Care: Use your legs, not your back, when lifting heavy sheets to avoid strain.
- Maintain Stability: Make sure that the area where you are moving the plywood is stable and free of obstructions.
- Report Any Damage: Inspect sheets for any damages before use; damaged plywood should not be utilized as it may compromise structural integrity.
Best Practices for Storing Concrete Form Plywood
Effective storage can greatly prolong the life of concrete form plywood. Here are some best practices:
- Store Off the Ground: Keep plywood on pallets or a raised platform to prevent moisture absorption from the floor.
- Protect from Elements: Store in a dry, sheltered area away from direct sunlight and excessive moisture.
- Stack Properly: Stack sheets flat, with the face side up and evenly supported to prevent warping.
- Maintain Inventory: Regularly check and rotate stock to ensure the oldest material is used first.
Understanding the Importance of Quality Control
Beyond just handling and storage, it’s crucial to understand the importance of quality control in the lifecycle of concrete form plywood. Quality control measures should be in place from the moment the plywood is manufactured to its final application on a construction site. This includes evaluating the plywood for defects such as voids, delamination, or improper thickness, which can all affect the performance of the concrete forms. By ensuring that only high-quality plywood is used, contractors can avoid costly delays and safety issues during construction.
The Role of Environment in Plywood Longevity
The environment in which plywood is stored plays a significant role in its longevity and usability. High humidity levels can lead to mold growth and deterioration, while extreme temperatures can cause the plywood to expand or contract, leading to warping. It is advisable to monitor the storage environment regularly and implement climate control measures if necessary. Additionally, using moisture barriers or protective wraps can further safeguard the plywood from environmental factors, ensuring that it remains in optimal condition for future projects. Click here to find more about climate.
Installation Techniques for Concrete Form Plywood
Preparing for Installation
Before installation begins, proper preparation is crucial. Start by assessing the project area and ensuring it is clear and free of debris. Gather the necessary tools and equipment required for the installation, ideally including:
- Impact driver or drill
- Measuring tape
- Square for ensuring right angles
- Level for surface checking
- Reinforcement materials depending on your design
In addition to these tools, consider the environmental conditions that may affect your installation. For instance, if you are working outdoors, check the weather forecast to avoid rain or extreme temperatures that could compromise the integrity of the concrete. It’s also wise to have a plan for managing any potential water runoff or drainage issues in the area where you’ll be pouring the concrete. Proper planning can save you time and resources by preventing unforeseen complications during the installation process.
Step-by-Step Installation Guide
The following steps outline a common approach to installing concrete form plywood:
- Measure and Cut: Use accurate measurements to cut plywood sheets to the required dimensions, always wearing safety gear during the process.
- Build Your Forms: Assemble your forms using the cut plywood, ensuring that they are level and securely fastened.
- Add Reinforcements: Depending on the project, you may need to add steel reinforcements to support the weight of the wet concrete.
- Double-Check Measurements: As a final step, double-check all dimensions and levels before pouring concrete to ensure precision.
Once your forms are assembled and secured, it’s essential to consider the application of a release agent on the inside surfaces of the forms. This step will facilitate the easy removal of the plywood after the concrete has cured, preventing any damage to the finished surface. Additionally, if you are working on larger projects, it may be beneficial to use bracing techniques to provide extra support to the forms, especially in areas where the concrete will be poured at greater depths. This added stability can help prevent any bowing or shifting during the curing process, ensuring a smooth and successful installation.
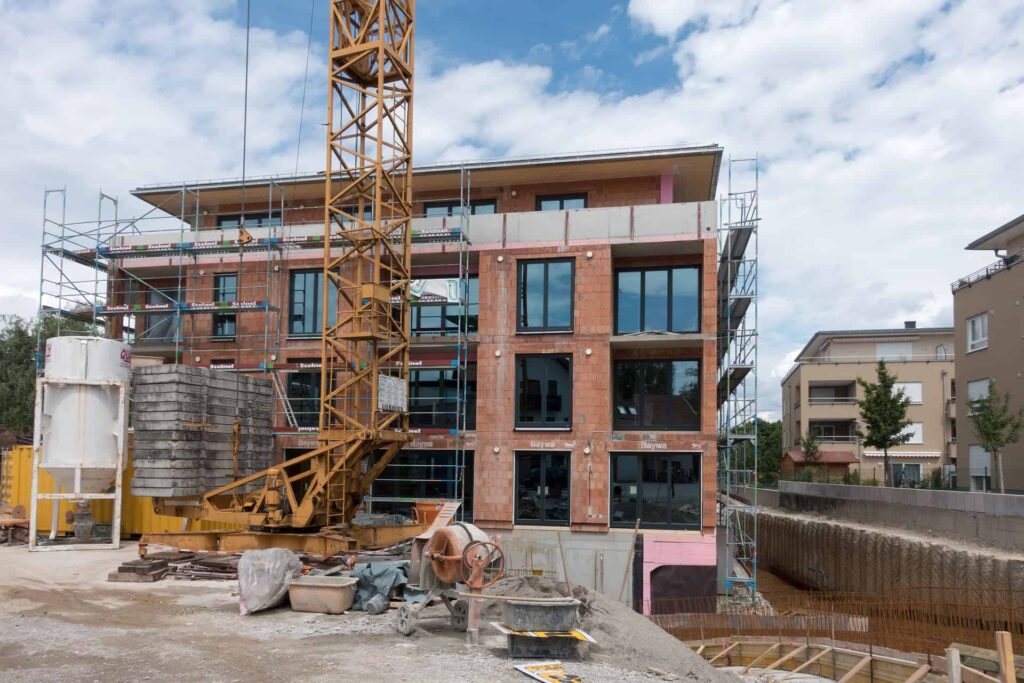
Maintenance and Durability of Concrete Form Plywood
Ensuring Longevity of Your Plywood
To extend the life of concrete form plywood, consider the following maintenance strategies:
- Avoid Heavy Impacts: Prevent heavy items from falling on the plywood, as impacts can cause significant damage.
- Keep Clean: Clean the surfaces gently after each use to remove dirt and debris, which can contribute to deterioration over time.
- Inspect Regularly: Regularly check for signs of wear, such as bowing or splitting, and address any damages immediately.
Routine Maintenance Tips
Routine maintenance can significantly improve the lifespan of your plywood. Here are a few additional tips:
- Utilize Water-Resistant Coatings: Applying a water-resistant sealant can further protect the plywood from moisture damage.
- Avoid Chemical Exposure: Protect plywood from acids and harsh chemicals that can degrade its quality.
- Store Appropriately After Use: Store sheets as previously mentioned to maintain their integrity when not in use.
In addition to the aforementioned strategies, it’s essential to consider the environmental factors that can impact the durability of your concrete form plywood. For instance, exposure to extreme temperatures can cause the wood to expand and contract, leading to warping. Therefore, if your project is located in an area with significant temperature fluctuations, it may be beneficial to invest in plywood specifically designed for such conditions. Moreover, using breathable covers during storage can help mitigate moisture buildup, which is particularly crucial in humid climates.
Read more at: The Role of Concrete Plywood in Durable Construction Projects